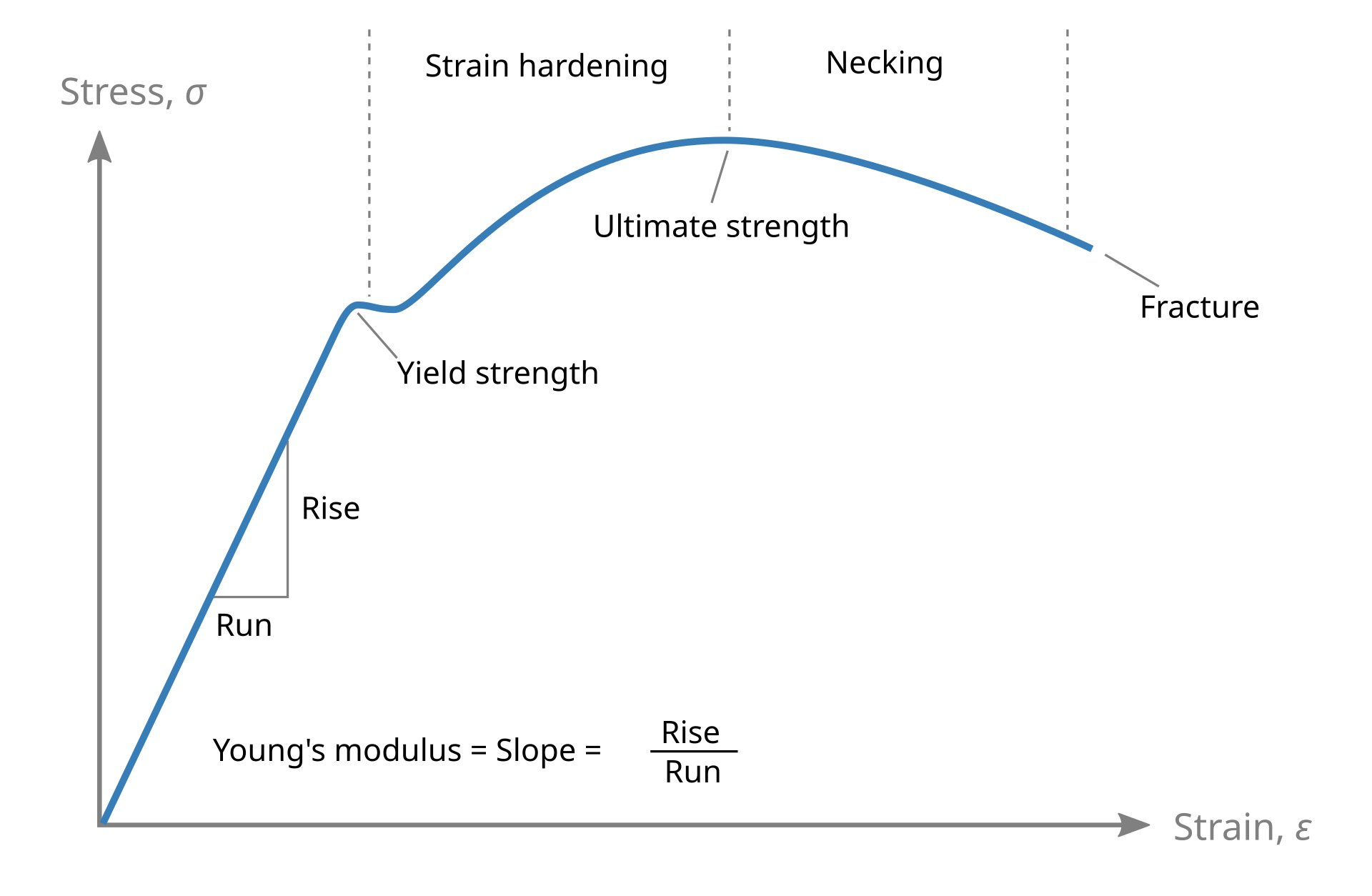
Key Takeaways
- Vibrations reveal a material’s elastic modulus through precise, non-destructive testing.
- By analyzing motion – especially the damping capacity – engineers can detect fatigue, find structural weaknesses, and maintain product quality.
- Natural frequencies captured during vibration tests link directly to Young’s modulus, allowing for fast and efficient modulus measurement.
- As a result, industries such as aerospace, civil engineering, and materials science rely on vibration-based testing for safety and innovation.
Understanding Vibrations: The Science Behind Motion
Vibrations are repetitive motions in materials and structures caused by external forces. Whether heard as sound or felt as movement, they reveal internal material behavior. Consequently, by examining responses—from the hum of a loaded bridge to the ring of a metal rod—engineers can evaluate stiffness and elasticity. In this post, we explore how vibrations uncover a material’s elastic modulus.
What Is Elastic Modulus and How Do Vibrations Reveal It?
Elastic modulus describes a material’s resistance to deformation under load. It is commonly quantified by Young’s modulus, which defines how much strain results from a given stress. The higher the modulus, the less the material deforms.
When a solid object vibrates, its natural frequency and amplitude depend on its stiffness, mass, and geometry. Therefore, every material has unique resonant frequencies that reflect these characteristics.
The Impulse Excitation Technique (IET) measures these frequencies. A light mechanical impulse sets the object vibrating. A sensor records the response. Then, with the object’s shape and mass known, Young’s modulus can be calculated—quickly and without causing damage.
Why Non-Destructive Modulus Measurement Matters
Traditional methods, such as tensile testing, often damage the specimen or require extensive preparation. In contrast, vibration-based testing allows you to evaluate actual components in their working form. As a result, you can:
- Verify integrity without destruction
- Inspect 100% of critical components
- Accelerate quality control while reducing cost
Because of these advantages, IET is especially valuable in safety-critical sectors such as aerospace and infrastructure. Furthermore, it supports sustainability by reducing testing waste.
From Motion to Modulus: Connecting Frequency and Young’s Modulus
Young’s modulus is a fundamental measure of material elasticity. Since resonant frequency depends on this modulus, IET enables its calculation through three simple steps:
- Apply a light mechanical impulse.
- Record the resonant frequency using a sensor.
- Use the object’s mass and dimensions in a standard formula to compute Young’s modulus.
As a result, modulus evaluation becomes fast, accurate, and practical in both R&D and production environments.
Real-World Examples of Vibration-Based Modulus Measurement
- Civil Engineering: Detect fatigue or micro-cracks in beams before deployment.
- Automotive: Verify stiffness of drive shafts and engine parts without destroying samples.
- Aerospace: Ensure turbine blades and fuselage sections meet stringent modulus requirements.
The Future of Material Testing: AI and Automation
Automation and AI are transforming vibration analysis. With modern systems, you can:
- Automatically interpret complex resonance data
- Predict mechanical failure trends before they escalate
- Integrate results with digital quality management platforms
Ultimately, this makes the testing process more consistent, efficient, and scalable.
Advantages and Limitations of Vibration-Based Modulus Testing
Advantages: This technique offers fast, non-destructive measurement of elastic modulus and is suitable for real-world components without special preparation. It also scales well for both lab and production environments.
Limitations: While modulus calculation for irregular shapes can be more complex, it is still feasible using shape factors. In some cases, data capture may require automation to maintain consistency across high-volume testing.
Applications: Where Modulus Testing via Vibration Delivers Impact
- Manufacturing Quality Control: Assess stiffness in every component rapidly and reliably.
- Research and Development: Evaluate new material performance in real time.
- Infrastructure Health Monitoring: Reveal hidden structural degradation before failure occurs.
Getting Started: Equipment and Approaches
To implement vibration-based modulus testing, follow these recommended steps:
- Use specimens of consistent geometry where possible.
- Choose an impulse excitation device suited for your material type.
- Apply standard measurement and modulus calculation procedures.
- Use automated software for consistent analysis and reporting.
FAQ
How do vibrations reveal the elastic modulus of a material?
Vibrations generate resonant frequencies that reflect material stiffness. Consequently, by measuring these frequencies, you can compute the elastic modulus directly.
What is Young’s modulus and why is it important?
Young’s modulus measures how much a material resists deformation. Therefore, it plays a vital role in material selection, safety, and performance design.
What are the benefits of non-destructive vibration testing?
It allows full-scale property evaluation without harming components. In turn, this saves time, reduces cost, and prevents waste.
Which industries benefit most from vibration-based testing?
Industries like aerospace, automotive, civil engineering, and materials science use it to ensure reliable, high-performing products.
How accurate is modulus measurement via vibration?
With proper calibration and suitable sample shapes, vibration testing delivers highly accurate modulus data.
Can vibration testing detect defects?
Yes. Changes in vibration behavior often indicate cracks, fatigue, or internal flaws.
Where can I get more information?
Contact our team for expert support, training, and equipment guidance.
Ready to Measure Smarter?
Maximize your testing accuracy with non-destructive modulus analysis. With IET, you get fast, reliable measurements—backed by modern automation and real-world performance.