Impulse Excitation vs Destructive Testing
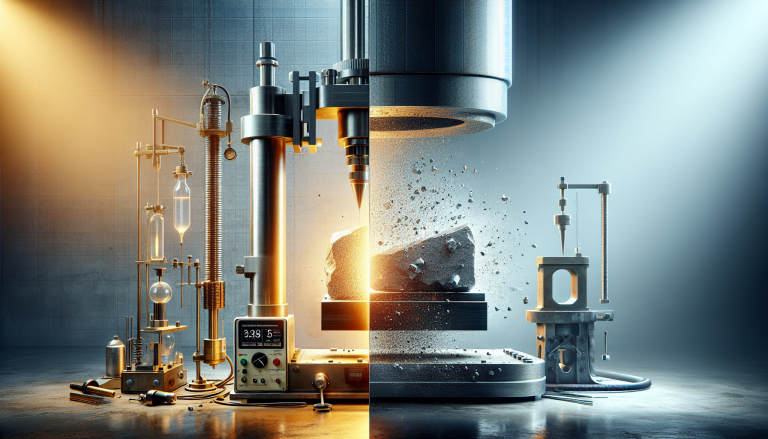
In the realm of material testing, understanding the difference between impulse excitation and destructive testing is crucial. Impulse excitation offers a non-invasive approach, allowing for real-time assessment of structural integrity without compromising the material. Conversely, destructive testing provides definitive results through the material's breaking point but at the expense of its usability. By prioritizing impulse excitation, we embrace a philosophy of measuring reality over mere assumption, leading to safer and more efficient engineering practices.